What an AI-Powered BMS Actually Delivers: Engineering Advances and Technical Insights
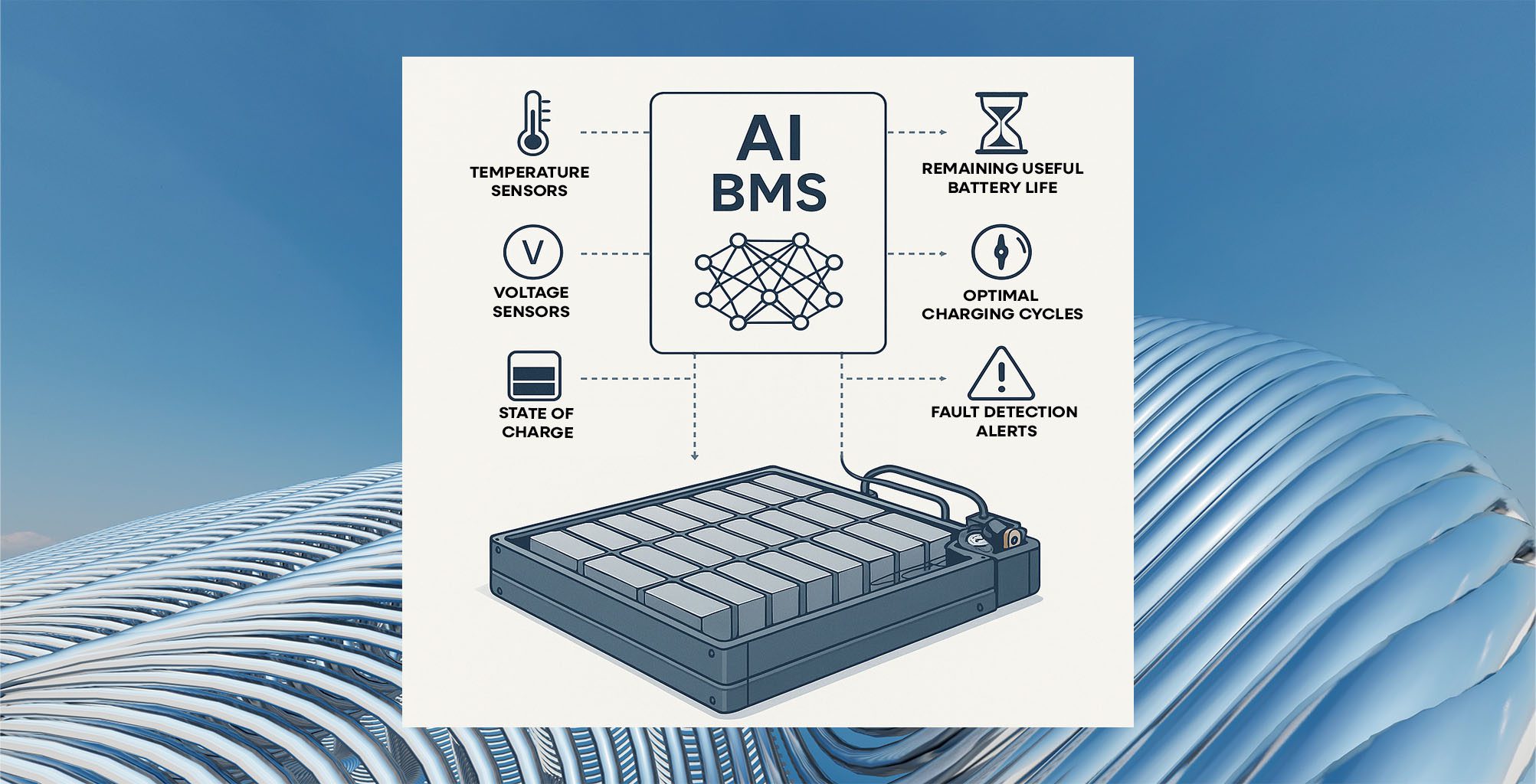
“AI-powered BMS” is a term we hear more and more frequently. In the broader AI world, we see the landscape evolving through distinct phases – most recently captured by Andrej Karpathy as Software 1.0 (hand-coded logic), Software 2.0 (deep learning), and the emerging Software 3.0, where we interact with foundation models through prompts rather than fixed network weights.
But does Software 3.0 – this new paradigm of flexible, prompt-driven intelligence – mean anything practical for battery management today?
The answer: Not yet. Before battery management can realise that next leap, our field must first master Software 2.0 – systems where deep neural networks, guided by battery domain expertise, replace hand-crafted rules for real-world decision-making. If you’ve seen Wayve’s AV 2.0 – where deep learning absorbs vast driving data to generalise across environments – the analogy is clear. For BMS, the goal isn’t to replace battery engineers, but to train neural networks, grounded in expert battery science, to “learn” from laboratory experiments, diverse fleet data, and operational edge cases.
So what does an AI-powered BMS do differently, and why does it matter?
1. SOC and SOH: Learning Beyond the Limits of the Lab
Traditional BMS software delivers robustness within the specific environmental ranges and cell types it was originally calibrated for. For example, conventional SOC and SOH estimation depends on carefully tuned look-up tables, often built from exhaustive cell characterisation campaigns performed in controlled laboratory settings.
However, this approach quickly hits its limits in production and field use. Chemistries like LFP present notoriously flat open-circuit voltage curves and significant hysteresis, making SOC estimation based solely on voltage and current challenging. Batteries in the field also drift from their initial state due to aging, manufacturing variability, and the broad spectrum of real-world operating conditions – ranging from temperature fluctuations and variable load profiles to differing charge/discharge patterns and usage behaviours.
Our AI-powered BMS addresses these limitations by deploying deep neural networks that are trained not just on synthetic or idealised data, but on vast, real-world datasets – spanning laboratory cycling, heterogeneous fleets, and multiple operational scenarios. The models blend learned battery behaviour with expert-engineered features, allowing them to infer SOC and SOH from high-dimensional sensor data. They adapt to temperature, cycling history, charge/discharge profiles, and even capture nuanced, cell-level drift – such as subtle, inconsistent changes in capacity or performance that develop across individual cells within a pack or fleet due to manufacturing variation, usage patterns, and aging. This results in:
- Improved SOC estimation for chemistries like LFP, which are difficult to model with traditional techniques
- SOH and RUL (remaining useful life) predictions that reflect actual usage and field degradation, not just lab curves
- Adaptation to real-world conditions without constant recalibration for each new pack, chemistry, or deployment
2. Diagnostics: Pattern Recognition at the Edge
Threshold-based fault detection remains essential, but it is fundamentally limited in its ability to anticipate rare or emergent failure modes. AI-powered BMS platforms extend this with machine-learned models that analyse high-dimensional, multi-modal time-series data generated by the battery – looking for patterns and anomalies invisible to rule-based logic.
This enables:
- Early detection of incipient faults, such as lithium plating, cell imbalance, or thermal instability, based on subtle signatures in the data stream – learned by blending battery science with large-scale data
- Reduction of false positives, so maintenance teams can focus on true emerging risks instead of nuisance alarms
- Diagnostic models that evolve as new data is collected, continually improving sensitivity and specificity through ongoing learning
For example, where traditional logic may only react to a cell voltage exceeding a threshold, an AI-powered system can recognise an evolving degradation trend by analysing patterns over thousands of operational cycles, alerting operators days or weeks before conventional systems would trigger.
3. Edge and Cloud: Enabling Continuous Improvement
A critical enabler for AI in BMS is the convergence of advanced embedded hardware and modern cloud infrastructure. The latest automotive grade microcontrollers and system-on-chips provide the performance needed to run deep neural networks on-vehicle – processing sensor data in real time for safety critical decisions.
At the same time, cloud infrastructure offers robust data pipelines, fleet-level storage, and advanced model management. This enables a closed learning loop:
- Edge (vehicle): Real-time inference using compact, battery-expert-guided neural networks, delivering high performance and responsiveness under all conditions.
- Cloud: Aggregation of anonymised fleet data, large-scale model retraining, and seamless deployment of updated models and strategies back to the edge.
With this feedback loop, the system leverages both domain knowledge and new operational experience. As new chemistries, pack designs, or failure modes are encountered in the field, the central AI can learn from the full breadth of fleet data, continuously refining its models and raising the standard of performance and safety across all deployments.
4. The Road Ahead: From Software 2.0 to Fleet Intelligence
The broader AI community shows that systems learning from data – rather than relying solely on fixed rules – consistently outperform legacy approaches in complex, variable environments. Just as autonomous driving AI tech copies human drivers, and Software 2.0 leverages neural networks for tasks too complex to hand-code, the next leap for BMS will come when we harness truly global fleet intelligence.
That’s the promise of Software 3.0 in batteries: central AI agents in the cloud, digesting billions of fleet data points, will one day deliver proactive, autonomous optimisation for performance, lifetime, and safety – across every cell, pack, and application. But to get there, the real engineering lift is happening today with AI-powered BMS: more accurate SOC/SOH, smarter diagnostics, accelerated validation, and an architecture designed for continual improvement.
References
This article was originally written for BatteryDesign.net, a leading knowledge hub for battery engineers and electrification professionals. If you’re interested in in-depth technical content, practical design insights, and the latest developments in battery technology, we highly recommend exploring their site.